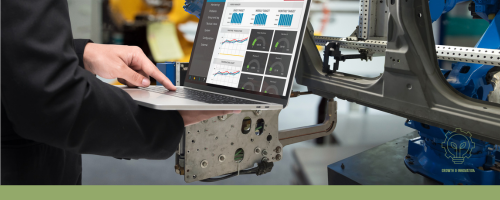
5 Ways Automation Drives Growth & Strengthens Your Workforce
Manufacturers are facing a workforce automation revolution. The Small and Medium Manufacturing Study: Robotics and Technology Engagement confirmed that the top organizational challenges faced by manufacturers today are labor costs and problems hiring and retaining production workers. While every manufacturer is different, implementing robotics and technology often directly addresses these challenges.
Advanced technologies such as robotics and automation are innovating the workforce. Automation can improve your manufacturing workforce by programming repetitive tasks and directing business procedures. However, the recent use of automation in the workplace has left many manufacturers questioning how this will affect their workforce.
Below are some ways in which automation can help solve workforce challenges and accelerate your adoption of always-advancing technologies.
1. Opportunities For More Intellectually Stimulating Jobs
The primary concern about implementing automation is the reduced demand for existing jobs. Automation can reduce the need for human services where tasks are mundane and repetitive. Different positions, such as assembly jobs, data entry, or customer service representation, can require little to no human labor.
This poses a serious concern as employee retention is essential for company quality and success. However, relying on automation to complete these repetitive jobs can allow your employees to undertake more challenging and intellectually stimulating tasks, ultimately increasing employee retention.
Rather than dedicating time to entering data, conducting manual calculations, or repeating tedious industrial tasks, automation opens the door for other opportunities that benefit your business and enhance the workday. Whether creating relationships with new clients, helping existing customers, or creating quality products with greater detail and precision, automation allows your employees to improve your services and products.
2. Reduced Costs and Reliability
Automation brings with it many benefits, one of which is reduced costs. Using machines for different jobs costs less than paying individual workers and produces more results. Machinery and technology don't need breaks, vacation days, or other conditions that employees typically factor into their job. Machinery and other systems can provide reliability in ways that employees cannot.
Additionally, automation produces a greater output in both quality and quantity, increasing your cost/benefit.
Robots and cobots perform tasks at a higher rate than people since they are programmed to repeat activities. While it is true that machines come with their price, the consistency, reliability, and productivity supplied, if implemented correctly, can outweigh the operational costs. With these reduced costs and increased dependability, your company can direct funds to other areas.
Reduced costs bring many benefits and opportunities. With newly directed funds, your business could afford to hire more employees with higher quality training (OR invest in developing high-quality training or apprenticeships internally, which increases your business efficiency in work and services). Automation is essential to workforce development and employee retention as it provides different avenues for your business to grow in quality and quantity.
As manufacturers integrate workforce automation, strategic planning is key. Our consulting services help manufacturers seamlessly implement automation while keeping employees engaged, improving retention, and ensuring long-term ROI.
3. Reduced Errors
Repetitive manual labor increases margins of error. Monotonous tasks can result in less attention to detail and a wandering mind. No matter the competence or ability of your employees, by repeating routine tasks throughout the day, they are prone to error. Since robots and cobots are programmed to complete a specific task repetitively, the margin of error decreases significantly. Machines and technology don't make the same mistakes manufacturing workers do. Automation ensures an accurately generated product through consistent programming production and thoroughly followed procedures. Automation also provides quality assurance in many ways.
By generating a higher range of more intellectually stimulating jobs, margins of error are reduced, more predictable, and more preventable.
With fewer margins of error and more time to focus on employee work, you can better supply your employees with the necessary tools and support to increase productivity. Better oversight of employee production can allow you to identify processing issues, monitor results, and implement better procedures.
4. Increased Workplace Safety
Automation also increases safety for employees in the manufacturing workforce. Those who work in factories with heavy machinery or hazardous equipment are subject to dangerous encounters. Repetitive tasks can lead to complacency, increasing the potential for personal injuries and workplace accident claims. Workplace incidents can result in injured employees, liability claims, and loss of funds.
Not only this, but employee safety concerns can also turn potential workers away from your business and present a negative image. Automating these jobs can provide employees with a greater sense of safety by preventing them from engaging in high-risk situations. Fewer workplace injuries mean decreased accident and liability claims and better safety precautions.
5. Higher Productivity and Increased Quality
As mentioned before, automation increases productivity. By transitioning to machine and technologically operated systems, employees can focus on more comprehensive and challenging work, ultimately providing better services. Automation can produce more products and reduce the workload of your employees. Consequently, this allows employees to focus on more specific and targeted areas. These improvements, coupled together, increase productivity in sales and service while ensuring employee retention.
The Bottom Line: Automation Enables Companies to Generate More Goods
Producing substantial sales opportunities and sustained growth increases the need for a highly trained and growing workforce. While many believe automation can take away available jobs, replacing jobs with automated systems can provide more opportunities for workers.
Successful businesses need successful strategies, which are highly attainable through integrating automation into your workforce. With improved quality and quantity production, your company can generate significant employee retention and workforce development through better time management, increased workplace safety, and necessary employee support.
How Can Manufacturers Adapt?
Automation is revolutionizing the workforce, driving innovation and efficiency. A skilled workforce is more essential than ever to stay competitive.
At Impact Washington, we help Washington manufacturers navigate automation with confidence. Our expert consultants develop tailored solutions to enhance productivity, retain skilled workers, and drive long-term success. Whether you're exploring automation or refining existing systems, we’ll help you stay ahead.
Workforce automation is the future of manufacturing. The real question is—how will your business adapt?