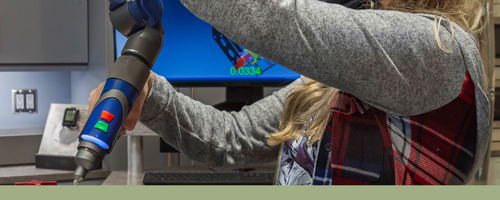
With the fourth industrial revolution focusing majorly on manufacturing process enhancement through the internet of things (IoT), cybersecurity systems, artificial intelligence (AI), and cloud computing, SMEs act as critical contributors to the Washington economy due to their significant contribution to the areas of productivity, trade, and employment.
Some small- and medium-sized businesses believe they're at a fundamental disadvantage in Industry 4.0, primarily due to the resources at their disposal. We've helped many who've seemed overwhelmed, then stuck, putting off tech for a future day. Research reveals that SMEs have much to gain in evaluating and adopting Industry 4.0. Let us help you create a cost-effective roadmap for success.
__________________________________________
Digital Transformation on a Small-Business Budget: It Can Be Done - article first appeared on Feb. 2, 2023, in Industry News is authored by Ethan Karp president & CEO MAGNET (the Manufacturing and Growth Network), an Ohio Manufacturing Extension Partnership. a sister Center to Impact Washington -NIST MEP
Since 2011, more than 200,000 academic papers have mentioned Industry 4.0, a staggering data point of the fourth industrial revolution’s rising influence. More than half of those mentions—about 105,000—came in 2020 and 2021 alone.
In other words, the research has matured. But the implementation, especially among small and medium-sized manufacturers, is still getting there.
I have a theory for that, one educated by years of work at MAGNET, the manufacturing consultancy I head in Northeast Ohio that is part of the Ohio Manufacturing Extension Partnership.
Most small- and medium-sized businesses believe they’re at a fundamental disadvantage when it comes to Industry 4.0, largely due to the resources at their disposal. They get overwhelmed, then stuck, putting off tech for a future day. They figure they can’t throw millions of dollars into a technological revamp or build a new, state-of-the-art facility anyway. And perhaps some of them are just a bit headstrong, having done things the same way for years or decades.
But all that research reveals there’s much to be gained. Even better, concerns about costs—at least to get the ball rolling—are largely overblown.
Here’s a full breakdown on how small and medium manufacturers can approach Industry 4.0, and what they stand to gain.
What are the benefits of Industry 4.0 for small and medium-sized manufacturers?
The simple answer, over the long haul, is that putting Industry 4.0 technologies into play will save money and increase efficiency. You’ll gain a much deeper understanding of the tools and machinery making up your factory floor, with analytics and insights that can be turned into actual business value.
You’ll make more informed decisions, increase output as well as surge capacity, and—crucially—become much more resilient to supply chain disruption. In fact, six months into the pandemic, 94% of manufacturers said Industry 4.0 had helped keep their operations up and running, McKinsey says.
How long will it take for those benefits to kick in?
Some technologies will show results almost immediately. For others, it takes a bit of time to reach maturity and capture the benefits.
When it comes to monitoring real-time data, for instance, the initial return on investment will come quickly. You’ll capture deeper insights as you have more data to pull from, but installing sensors throughout your operation to track and analyze performance will provide immediate upside. You’ll be able to assess things like vibration patterns, pressures, temperature and cooling rates, connecting to benchmarks or historical data to get a view of how equipment is performing. That will help you optimize operations and stay proactive about maintenance, reducing downtime.
How much does it cost to implement Industry 4.0 technologies?
Not to go all infomercial on you, but prices may vary. In fact, they absolutely will, depending on how much you choose to put in place. Some massive manufacturers even create brand new, state-of-the-art facilities to capture all the value of Industry 4.0.
But it’s often not realistic for smaller manufacturers to go all in right away. The beauty with implementing these technologies is that they build on each other, one investment leading into the next.
Start by installing sensors to make your manufacturing operation trackable, and you may spend just a few thousand dollars while giving yourself access to analytics that will take money off your expense line.
Once you’ve gotten your feet under you, you may decide to overhaul the technology capabilities of your manufacturing. I’m not here to claim that won’t be expensive, but even these overhauls can be done in phases to reduce the cost burden. You may choose to start with just a single cobot—or collaborative robot—before moving on to entire sections of your manufacturing floor. Rinse and repeat until you’ve optimized the entire warehouse.
Or, mix in advanced technology like artificial intelligence, machine learning and virtual reality as you update how you attract new talent and upskill your existing teams. The options are abundant, and they come at a wide variety of price points.
Are the results quantifiable? How can I know my investment will be worth it?
Consider that, as McKinsey determined earlier this year, “it is not uncommon to see 30 to 50% reductions in machine downtime, 10 to 30% increases in throughput, 15 to 30% improvements in labor productivity and 85% in accurate forecasting.”
Of course, beyond those high-level numbers are stories that show the returns on a granular level. Industrial bellow-maker Allow Precision Technologies, for instance, has implemented Industry 4.0 technologies including machine monitoring and scheduling, machine tending, automation and optical part inspection. The system has led to improved machine utilization—resulting in a double-digit-percent improvement in man-to-machine ratio and production rate.
Bowden Manufacturing, a 70+-year-old machine shop in Willoughby, Ohio, offers another success story. The company implemented a monitoring system that has helped measure machine downtime, create accurate production-time estimates, quickly identify issues on the shop floor and improve data collection and analysis. “The ROI is challenging to measure, yet there are at least four or five factors in the system we use that unequivocally makes it worth it,” says Andy McCartney, president at Bowden. “Our team is centered around this data that we see every day.”
Manufacturers shouldn’t think twice about simply diving in, researching certain technologies, and figuring out how to implement within their companies. As mentioned, real-time data monitoring offers a low-cost starting point that can snowball into bigger and better things. The more you do, the more you learn, and the more confident you’ll feel about future implementations.
There are also many people and organizations out there who can help guide you along your technology transformation journey. Find a local consulting firm, Manufacturing Extension Partnership, or mentor with experience helping small-to-medium-size manufacturers implement Industry 4.0 technologies and bring them into your world.
Diving into Industry 4.0 technologies can feel risky, but, in reality, manufacturers who would like to stay relevant and competitive over the next decade have no other option. The good news is that such investments can be done gradually to steer clear of a one-time, enormous cost burden. A step-by-step approach also allows leadership to gain greater understanding of often complex technologies and systems, snowballing into more successful implementations as time goes on.